Mold Injection Service
Zhuofei Technology provides high-quality mold injection services, focusing on producing high-quality end-use parts to meet various production needs. As a leading mold injection service provider, Zhuofei Technology uses advanced injection molding technology and high-precision molds to produce plastic parts that meet strict quality standards.
The high-quality mold injection molding service provided by Zhuofei Technology has the following significant characteristics in terms of performance indicators: using high-precision molds and injection molding technology to ensure that the component size tolerance is controlled within ±0.05 mm. It can accurately reproduce complex geometric shapes and subtle design details; provide high-quality surface treatment, including smooth surface and high gloss, to ensure that the parts meet the customer's high standards for surface quality. The surface roughness can be controlled within the range of Ra 0.8-1.6μm.
Upload your 3D file to get a quote
Get real-time quotes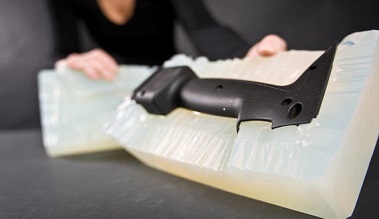
Vacuum Casting Polyurethane Resins |
||||||
Material Simulation |
Strength Shore |
Flexion(MPA) | TC Max |
Product Color Description |
Advantage Disadvantage |
Shrinkage |
ABS TYPE | ||||||
ABS | 83 shD | 1790 | 85 | Amber, white and black | Good resistance | 1 |
ABS | 81 shD | 2200 | 93 | Dark Amber | Good resistance | 1 |
PS chocs | 74 shD | 1500 | 70 | White/Black | Ideal | 1 |
POLYPRO TYPE | ||||||
PP | 75-83 shD | 600-1300 | 70 | White/Black | Good resistance | 1 |
COLORABLE ELASTOMERS | ||||||
Elastomer | 20-90shA | / | / | Milky white/Black | Good Blend | 1 |
Elastomer | 30-90shA | / | / | Clear | Good Blend | 1 |
HIGH TEMPERATURE | ||||||
PC | 85 shD | 2254 | 105 | White/Black | High T℃ 105° | 1 |
PS/ABS | 80 shD | 2300 | 120 | Black | IdealTG 120° | 1 |
UL-VO | ||||||
ABS | 83 shD | 1800 | 85 | White | 94V0 flame retarding | 1 |
Loaded ABS | 87 shD | 3300 | 100 | Off White | V 0 far 25 | 1 |
CLEAR | ||||||
PMMA | 87 shD | 2100 | 100 | Clear | Coloration TG100° | 0.996 |
Available Finishes for Mold injection Parts
Parts have a smooth, satin-like finish due to the master pattern being bead-blasted matte. Clear and translucent parts with this finish will appear frosted. Matte finishes are useful for handheld and high-touch areas as it reduces fingerprint visibility.
A finish that includes some sheen but not high reflectivity. Semi-gloss finishes are in between high-gloss and matte, resulting in a smooth, easy-to-clean surface.
A highly reflective finish is made by polishing the master pattern before making the mold. High-gloss has a high sheen and will have the highest transparency for clear parts. High-gloss is useful for cosmetic models, cleanable surfaces, and lenses.
Zhuofei can provide additional processing, including custom textures, secondary finishes, painting, and more.
Mold injection Options
Polyurethanes can be blended with pigments to achieve a variety of colors. Naturally, a urethane may be amber to milky-white in color. Zhuofei’s clear urethane options are formulated to be colorless. Below are Zhuofei’s color options:
- Black
- Color-Match
- Natural (unpigmented)
- Clear (colorless)
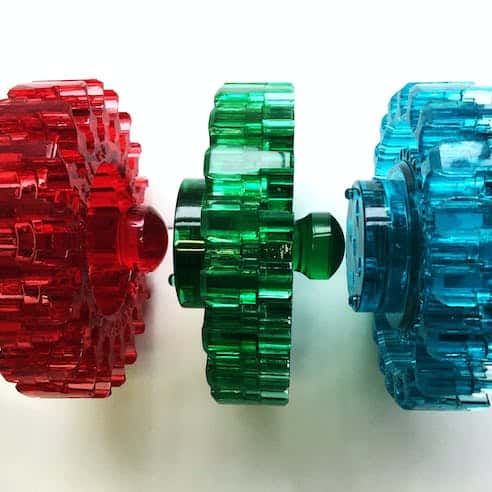
Overview: What is mold injection molding?
Injection Molding is a production process commonly used to manufacture plastic parts. This process forms various complex shapes of parts by injecting molten plastic into precision-made molds. The following are the basic processes and main features of mold injection molding: It can produce parts with high precision and complex geometric shapes. The mold design and manufacturing accuracy determine the quality of the final product; it is suitable for mass production, with a short production cycle, and can produce a large number of parts in a short time; various thermoplastics and thermosetting plastics can be used to meet different application requirements.